Ammonia (NH3)
Physical and chemical properties
- Chemical formula: NH3
- Relative molecular mass: 17.03
- Gas constant: 448.21 J/kg·K
- Boiling point at 101.3 kPa: -33.3°C
- Melting point: -77.7°C
- Critical temperature: 132.25°C
- Critical pressure (abs.): 114.2 bar
- Solubility in water: up to 74,301 ml in 100 g H20 at 20°C
Impact on human beings and environment
Ammonia is a toxic flammable refrigerant in B2 safety group according to GOST EN 378-1-2014, and B2L group according to GOST 33662.1-2015 (ISO 5149-1:2014)).
Auto-ignition temperature is 630°C, flame propagation velocity is 8 cm/s. As the lower flammability limit (LFL) of ammonia, a minimum concentration required for ignition is 0.116 kg/m3 is taken.
Concentrations from 15 to 28% create the risk of explosion. Pungent smell indicates ammonia leakage long before the explosive concentration is reached. In the open air, such a concentration cannot be achieved because ammonia is lighter than air and when leaked escapes.
Reactions with mercury, halogens, hypochlorites, nitrogen oxides, and some organic compounds, result in formation of explosive and unstable compounds.
Ammonia threshold limit value (TLV) according to SanPin 1.2.3685-21
- The air of residential area:
- maximum single exposure up to 20–30 min.: 0.2 mg/m3,
- average daily exposure below 24 hours: 0.1 mg/m3,
- average annual chronic exposure below 1 year: 0.04 mg/m3.
- The air of working spaces:
- 20 mg/m3.
The odor threshold is 0.5 mg/m3. At concentration 40–80 mg/m3, ammonia irritates eyes and upper airways, provokes headache. Exposure to 1500–2700 mg/m3 during 0.5–1 hour may cause death.
- Ozone-depleting potential (ODP): 0.
- Global warming potential (GWP): 0.
Production of ammonia
In industry, ammonia is produced through the Haber process developed by Fritz Haber and Carl Bosch by the reaction of nitrogen gas and hydrogen gas using a catalyst (porous iron with aluminum oxide, potassium oxide, and calcium oxide) under high pressure and temperature. Generated ammonia is removed through cooling, and unreacted nitrogen and hydrogen are returned to the synthesis column.
The industrial production of ammonia is a power-consuming process. According to USA researchers, about 4,700 kW·h of thermal energy, 415 kW·h of electrical energy, and 6,300 kWh of energy stored in the methane used in the synthesis process are consumed for the production of 1 ton of ammonia.
Ammonia used as refrigerant is 99.98% pure (A grade) and contains almost no water and other substances.
Use of ammonia
Ammonia has long been used in refrigeration equipment and is marked as R-717 in R-numbering.
Refrigeration with compressed ammonia was introduced by David Boyle in 1872 in the USA.
Carl von Linde built an ammonia compression refrigerating machine for a brewery in Trieste that then was a part of the Austro-Hungarian Empire, in 1876.
Ammonia was used as a refrigerant in the first domestic air conditioner manufactured in the United States in 1929. The refrigeration machine was located outside to prevent unpleasant odor in case of leakage, and cooled water was fed to an indoor fan coil.
Ammonia has higher volumetric refrigerating effect and heat transfer coefficient than those of synthetic refrigerants (CFC, HCFC, HFC), so pipes in ammonia systems may have a smaller diameter.
High solubility in water—one volume of water per 700 volumes of ammonia—prevents the system from moisture freezing.
A strong smell helps find leakages.
There are special requirements for materials used in ammonia refrigerating systems. Ammonia, especially in the presence of water, reacts with copper, zinc, their alloys, aluminum, stannic, and dissolves many resins and plastics.
Ammonia as a refrigerant is usually used in vapor compression and absorption refrigerating machines.
Ammonia absorption refrigeration
An absorption refrigeration machine is charged with a solution of ammonia in double-distilled water (ammonia mass concentration 4–36%). Added nitrogen creates back pressure to ammonia vapor.
The ammonia water is constantly heated by the boiler. As the boiling temperature of ammonia is much lower than that of water, evaporation leads to the release of condensed ammonia vapors. Vapored ammonia is partly condensed in the stripping column, a special heat-exchanger. The generated condensate ammonia streams down to the lean solution from the boiler, and the vapors with a higher concentration of ammonia enter the condenser. The high concentrated liquid ammonia leaves the condenser to enter the evaporator where it boils removing the heat of the refrigerating chamber. The lean solution from the boiler enters the absorber and is cooled by the surrounding medium down to the onset absorption temperature. The ammonia vapors from the evaporator enter the absorber too in the opposite direction to the cooled lean solution. Then the lean solution absorbs the ammonia vapors and releases some heat into the environment. The strong solution is pumped from the absorber to the boiler.
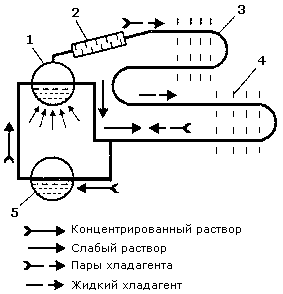
1 — boiler,
2 — stripping column,
3 — condenser,
4 — evaporator,
5 — absorber.
The solution and the refrigerant circulate continuously while the pump and boiler are operating. So, the suction function of a mechanical compressor is performed by the absorber, and the discharge function, by the pump.
In absorption refrigerating systems, exhaust heat of production processes and heat of combustion of cheap gas can be sources of power. The absence of moving parts and shutoff valves ensures the long useful life of the equipment and noiseless operation.
Ammonia refrigerating systems are used, for example, like domestic refrigerators. Refrigerator trucks are equipped with water-ammonia refrigerating systems that use waste heat of exhaust gas as a source of heat energy.
Ammonia adsorption refrigeration
Air-conditioning systems for passenger buses were developed in the USA. It is another example of an ammonia refrigeration system using the waste heat of exhaust gas.
In the adsorption refrigeration cycle (not absorption), the adsorbent, e.g. activated carbon, adsorbs the evaporated refrigerant at low temperature and pressure, and releases it at heating and high pressure. Compression is achieved by cyclic heating and cooling of the adsorbent and the refrigerant, creating an outgoing flow of the refrigerant under high pressure in the ‘hot’ phase of desorption (discharge) and an incoming flow under low pressure in the ‘cold’ phase of adsorption (suction). The opposite heating-cooling cycles in several adsorbers can create a continuous flow of the refrigerant. In such a case, each adsorber is fitted with one-way valves: one to duct the low-pressure vapors from the evaporator and prevent it from entering the high-pressure refrigerant, and another to duct the high-pressure refrigerant to the condenser and protect the adsorber.
This type of solution uses the waste heat of exhaust gas without taking off the effective power of an engine. Another advantage is a limited number of moving parts of the adsorption system; only valves are used thus reducing mechanical loss, noise level and extending the service life.
Ammonia vapor-compression refrigeration
In ammonia vapor-compression refrigerating systems, a vapor compression cycle is applied: the refrigerant removes heat from the cooled body and evaporates, then it is compressed by the mechanical compressor and condenses under high pressure transferring heat to atmospheric air or cooling water, and after that, the refrigerant passes the expansion device to enter the evaporator, and the cycle repeats.
Refrigerating systems can cool either directly or indirectly. In the first case, the evaporator removes heat from the cooled medium or body, in the second one, the primary refrigerant cools the secondary refrigerant fed to the heat exchanger of a cooled room or sprayed there to cool the air and cooled body.
Ammonia vapor-compression refrigerating systems can be of different designs.
Ammonia container refrigeration unit
With container refrigeration units, stationary machine room becomes unnecessary.
Units are designed as separate modules assembled into a single device with the evaporating condenser with an integral pump and a catcher for the recirculated cooling water.
Container refrigeration units can be used as chillers to supply cold to production lines and cool industrial premises, and as packaged condensing units with remote evaporators, including refrigerant pump circulation. As evaporators of container refrigeration units, the following devices are used:
- film evaporators for making ice water or cooling brine;
- slurry ice makers;
- flake ice makers;
- plate freezers;
- tunnel and spiral freezers;
- air-coolers of cooling and freezer rooms;
- other cold consumption technical facilities.
Ammonia onboard vapor-compression refrigeration
After the ban on the use of ozone-depleting substances in onboard refrigeration equipment of vessels built after January 1, 2020, entered into force, ammonia and carbon dioxide are in good demand for new onboard refrigeration equipment.
Processing onboard refrigerating plants are used for cooling and storing caught fish, making ice for fish cooling, freezing and storing frozen fish, cooling and storing salted and canned fish. The design of such plants provides for a separate refrigerating machine for each cooled object (or several objects with the same evaporation temperature).
Modern onboard refrigerating plants have a smaller refrigerant charge, 3–5 times less than a stationary plant.
The Russian Maritime Register of Shipping prohibits the application of ammonia for direct cooling of holds, so at vessels with ammonia refrigerating plants brine refrigeration is used at holds and tween-decks. Battery cooling is used to store frozen products, and air cooling to cool products.
Direct ammonia cooling is used to freeze fish and make ice.
According to the Russian Maritime Register of Shipping, ammonia refrigerating plants should be located in separate gas-tight premises with two exits, one leading to the open deck. If ammonia is used in machine rooms and premises for processing equipment, water sprinkling systems and water curtains are installed at exits, against ammonia leakage or fire.
The machine room must have an ammonia absorption system with exhaust and emergency fans, an ammonia absorption device, and a water tank. Ammonia concentration in the air of the machine room, exhaust ventilation of an ammonia absorption device, premises used to store ammonia stocks and emergency pipelines must be under continuous control.
Ammonia cascade systems
Ammonia refrigerating plants can serve not only as stand-alone units but as a high-temperature stage of cascade systems where carbon dioxide (CO2) is used in the low-temperature stage. Examples of such systems are described in a separate section.
Additional materials
- Mayekawa ammonia-pentane cascade heat pump will heat steam to 145°C for prawn producer Stella Polaris
- Hansen and HB’s new evaporator control sensor can reduce the ammonia charge in industrial systems by 75%
- District heating plant in historic German city uses ammonia heat pumps to generate heat from wastewater
- U.S. EPA announces final rule updating safety requirements for ammonia refrigeration
- Study finds R717/CO2 cascade refrigeration system offers 35% higher COP than R404A systems to Indian seafood processors
- Scantec provides centralized low-charge ammonia system for poultry distribution warehouse in Western Australia
- Evapco VP details the ESG benefits of packaged low-charge ammonia systems
- GEA supplies two-stage ammonia refrigeration system for U.K.’s tallest cold storage facility
- Ammonia seen as ‘Worthwhile’ for large-capacity HVAC&R projects in Latin America
- Bitzer support for low-charge ammonia chiller
- Experts call for more natural refrigerant case studies
- Star Refrigeration produces guide for transitioning to natural refrigerants like ammonia
- Combined thermal management is future of HVAC&R, says CIMCO refrigeration
- Canadian meat processor ‘Does what is right,’ cutting carbon emissions with ammonia heat pump system
- Glycol systems offer best ammonia reduction in analysis of oil cooling and evaporators
- ASHRAE and UNEP announce lower GWP award selections
- ATMO America: Evapco installs its first low-charge ammonia split systems in Nevada cold storage facility
- German life cycle assessment finds ammonia more environmentally friendly than synthetics or hydrocarbons for residential heat pumps
- Sorption process points to small-scale applications of ammonia refrigeration
- Scientist calls for use of natural refrigerants in ice slurry systems on fishing vessels
- Demonstration sites highlight potential of natural refrigerants in India
- Chillers using ammonia mix save over 744 metric tons of CO2e emissions at Slovak Tannery
- Packaged ammonia or CO2? Evapco now offers both
- Water consumption should be a “high priority” for operators of water-cooled HVAC&R Equipment, says BAC
- CTS improves ultra-low-charge ammonia chiller performance with ejector
- Evapco Reports Installation of 100 Low-Charge Ammonia Packaged Units at 25 Sites
- Greater awareness needed on benefits of low-charge ammonia systems in Australia, says Scantec
- Refrigerant Carbon Credits Plan Aims at Cutting Cost of NatRef Transition
- ATMO America: Cimco Ammonia System for Meat Processor an Early Example of ‘Net Zero’
- Mayekawa Installs First FUGU Ammonia Chillers in Germany, France & Spain
- GEA Heating & Refrigeration Technologies expands semi-hermetic product portfolio
- Industry refrigerant guidance outlines system efficiency and safety challenges
- Resolution of the conference “Natural refrigerant ammonia — Chemical and technical safety of the Russian Federation”
- New working fluid for the transformation of oceans’ heat energy (in Russian)
- Refrigerants and environment (in Russian)
- Flughafen Zürich. Approach to environment protection (in Russian)
- Energy and environmental paradigms of refrigerants (in Russian)
- Issues of safety enhancement of ammonia systems (in Russian)
- Use of ammonia refrigeration systems at the Balkan peninsula (in Russian)
- Use of ammonia in Africa, Thailand, China. Bangkok conference results (in Russian)
- Natural refrigerants in North America. Food supply (in Russian)
- Natural refrigerants for the future of Russia (in Russian)
- Natural refrigerants in North America. Transport (in Russian)
- 09.05.2013—11.05.2013, 5th IIR conference “Ammonia refrigeration technologies” (in Russian)
- Ammonia refrigerating plants in China (in Russian)
- Ozone-depleting substances and environmentally safe alternatives (in Russian)
- New technology for onboard freezing without ammonia pump (in Russian)
- Use of ammonia in the Russian refrigeration sector: problems and prospects (in Russian)
- Turkmenian ozone office in Moscow
- About natural refrigerants (in Russian)
- ATMOsphere technological summit to propose ammonia as an alternative to HCFC for all countries (in Russian)
- Conference “Natural refrigerant ammonia — Chemical and technical safety of the Russian Federation”
- Trends in the development of ammonia refrigeration systems (in Russian)
- Pros and cons of using eco-friendly refrigerants in refrigeration plants (in Russian)
- Natural refrigerants in North America. Industry and special uses (in Russian)
- R-717 and R-404A: advantages and disadvantages (in Russian)
- Ammonia will remain popular in the European market (in Russian)
- Research-to-practice conference “Improvement of reliability and efficiency of refrigeration and petrochemical equipment”
- Zurich airport. Use of natural refrigerant ammonia (in Russian)
- 16.10.2013, Conference “Natural refrigerant ammonia — Chemical and technical safety of the Russian Federation”
- Ammonia as refrigerant (in Russian)