Canadian meat processor ‘Does what is right,’ cutting carbon emissions with ammonia heat pump system
August 29, 2023
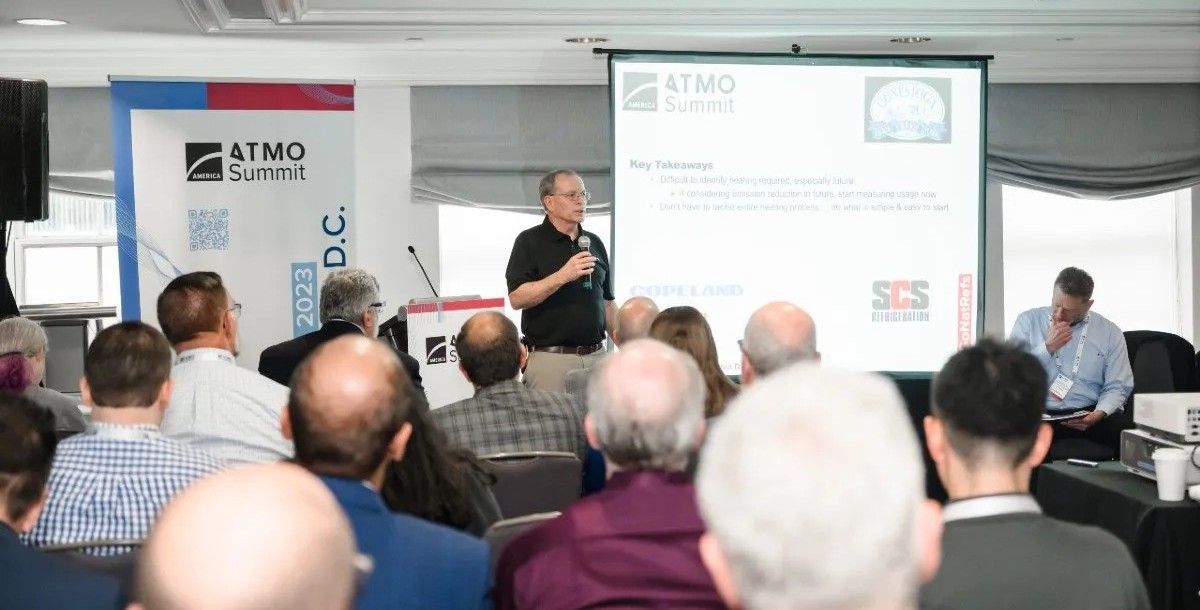
By using an ammonia (R717)-based heat pump system in place of a “mish-mash” R22, R404a and R507 refrigeration system, Canadian meat processor Conestoga Meats has cut its annual carbon emission by 3,000 metric tons over the past decade, according to U.S-based manufacturer Copeland (formerly Emerson), which supplied the R717 system.
In addition, the ammonia system, used for both heating and cooling, annually saves 3,374MWh of natural gas energy and 3.1 million gallons (11.7 million liters) of water previously lost from evaporative condensing.
Gary Chafee, Industrial Heat Pumps and CO2 Business Development Manager at Copeland, presented the installation and its associated long-term data at the ATMOsphere America Summit 2023, held June 12–13 in Washington, D.C. The event was organized by ATMOsphere, publisher of ammonia21.com.
Conestoga Meats started discussions about refrigerants and systems with the manufacturer in 2012, said Chafee, adding that the meat processor wanted to “reduce emissions, reduce energy and do what is right.”
Besides switching to a future-proof natural refrigerant, the meat processor sought to expand cooler capacity for increased business and required sufficient domestic 140°F (60°C) hot water for facility processing and cleanup. “The overriding function was that they didn’t want to have production shut down if they didn’t have enough hot water,” said Chafee.
The final design added cooling for a total capacity of 740TR (2,602kW) provided by Vilter-brand ammonia heat pumps. Two ammonia compressors provide 640TR (2,251kW) at 15°F (-9.4°C) saturated suction temperature (SST) for cooling and 95°F (35°C) saturated condensing temperature (SCT) for heating in a traditional ammonia system setup with evaporative condensers, said Chafee.
One compressor with a 99TR (348kW) capacity was set to a 20°F (11°C) higher condensing temperature with an SCT of 115°F (46.1°C), “which allowed us to make 100°F (37.8°C) hot water from it,” he added.
The 100°F hot water goes into a direct contact water heater – which handles instantaneous and rapid load changes – to boost the water temperature to the required 140°F. The company looked at using the heat pump to provide water above 100°F but decided that temperature was optimal after collaborating with the direct contact water heater specialist. Direct contact water heaters work best with a 40°F (22.2°C) lift, Chafee noted.
The system reclaims the waste heat with an ammonia heat pump skid that uses an R717 condenser. To prevent ammonia contamination in the potable water, an isolated glycol loop runs between the condenser and a plate heat exchanger to heat the potable water to 100°F.
The combined COP of the system is 6.19, with a COP of 3.15 for heating and a COP of 3.04 for cooling. “The overall payback for the system was a little under three years with incentives provided by the Canadian government and utility company,” said Chafee.
When reporting how the system is operating, Chafee referred to quotes provided by the end users.
“Since installed, this system has run for over 50,000 hours with no unplanned maintenance or lost production time,” said Rob Schneider, Plant Chief Operator at Conestoga Meats.
“In hindsight, the only thing that we might have done differently on the project was to install a larger heat pump as Conestoga has experienced healthy growth in their business over the last few years,” said Jason Short, President of SCS Refrigeration.
Lessons learned
Chafee noted key takeaways from this project in his presentation.
Identifying heating loads, especially future ones, seems to be a common issue, Chafee said, adding that he gets calls weekly from consultants hired by companies that want to be sustainable but do not have enough upfront data to design a heat pump system.
“A heat pump system costs millions of dollars, so spend a hundred thousand dollars and start measuring the temperature and other loads,” he advised. “That way, in a year from now, when you are serious about a carbon-friendly system, we have something to work with.”
Without the data, you might end up like Conestoga with a an undersized system, he warned.
Chafee also advised companies to start small. “You don’t have to tackle the entire heating process; start with what is simple and easy to do.” In addition, collaborate with everybody involved.
Lastly, he advised working on developing a culture of energy savings and CO2e emission reductions, especially among end users “because without that, it is going to be a financial decision at this stage with heat pump use in the U.S., and somewhat in Canada, with the natural gas option.”
In an end users’ panel at the summit, Chafee, in the audience, was encouraged to hear John DeCicco Jr., President and CEO of the New York-based food retailer DeCicco & Sons say, “I am comfortable with a three-to-five-year payback.”
“We need that culture that says, ‘Hey, we want to do what is right,’” said Chafee.
Copeland, a 100-year-old HVAC brand, manufactures compressors, heat pumps, controls, valves and other technologies for residential, commercial and industrial applications, including those using natural refrigerants like ammonia, CO2 (R744), and propane (R290).